The Role of Defoamers in the Chemical and Food Processing Industries
The Role of Defoamers in the Chemical and Food Processing Industries
Blog Article
Exactly How Defoamers Improve Effectiveness in Production and Manufacturing

Understanding Defoamers
Defoamers play a critical function in various producing procedures by effectively combating the formation of foam, which can impact and interrupt procedures item top quality. Foam can occur in many contexts, such as during mixing, home heating, or chain reactions, possibly resulting in ineffectiveness and incongruities in products. The device through which defoamers run usually includes lowering the surface tension of the fluid, permitting bubbles to rise and coalesce to the surface much more conveniently, where they can then burst.
Reliable defoamers not only reduce foam development however also keep compatibility with the product, ensuring that there are no damaging results on the final result. Comprehending the homes and functions of defoamers is crucial for makers aiming to enhance their procedures, boost productivity, and keep the integrity of their items (defoamers).
Key Benefits of Defoamers
Making use of defoamers in producing procedures provides a variety of significant advantages that boost functional efficiency and product top quality. One of the main benefits is the reduction of foam formation throughout production, which can obstruct machinery and disrupt workflows. By lessening foam, defoamers ensure smoother procedures, causing decreased downtime and maintenance expenses.
In addition, defoamers boost product uniformity by avoiding air entrapment, which can jeopardize the honesty of the end product. This is especially essential in sectors where aesthetic appearance and texture are important, such as in paints, coatings, and foodstuff. Improved product high quality not just fulfills consumer assumptions but also strengthens brand name credibility.
Additionally, defoamers can assist in maximizing source use. By boosting the efficiency of resources usage, they add to set you back financial savings and lowered waste, straightening with sustainability objectives. Last but not least, the application of defoamers can lead to shorter processing times, enabling producers to enhance production capacity without considerable capital expense - defoamers.
Applications in Various Industries
In manufacturing procedures throughout different industries, the application of defoamers plays an important role in enhancing performance and item high quality. These chemical additives are utilized in industries such as food and beverage, drugs, and textiles to reduce foam-related obstacles.
In the food and drink market, defoamers are crucial throughout the fermentation process, avoiding frothing that can interrupt production and ruin the product's stability. Likewise, in the pharmaceutical sector, defoamers are made use of in the formula of fluid medications, guaranteeing harmony and security while decreasing waste.
Textile production also takes advantage of defoamers, as they are utilized in coloring and completing procedures to promote also circulation of dyes and chemicals. This application not just improves the last item's appearance yet also minimizes the amount of water and energy eaten during production.
In addition, in the paper and pulp industry, defoamers assist keep process effectiveness by reducing foam that can impede equipment efficiency. In general, the varied applications of defoamers throughout these industries highlight their relevance in optimizing manufacturing procedures and delivering top notch products.
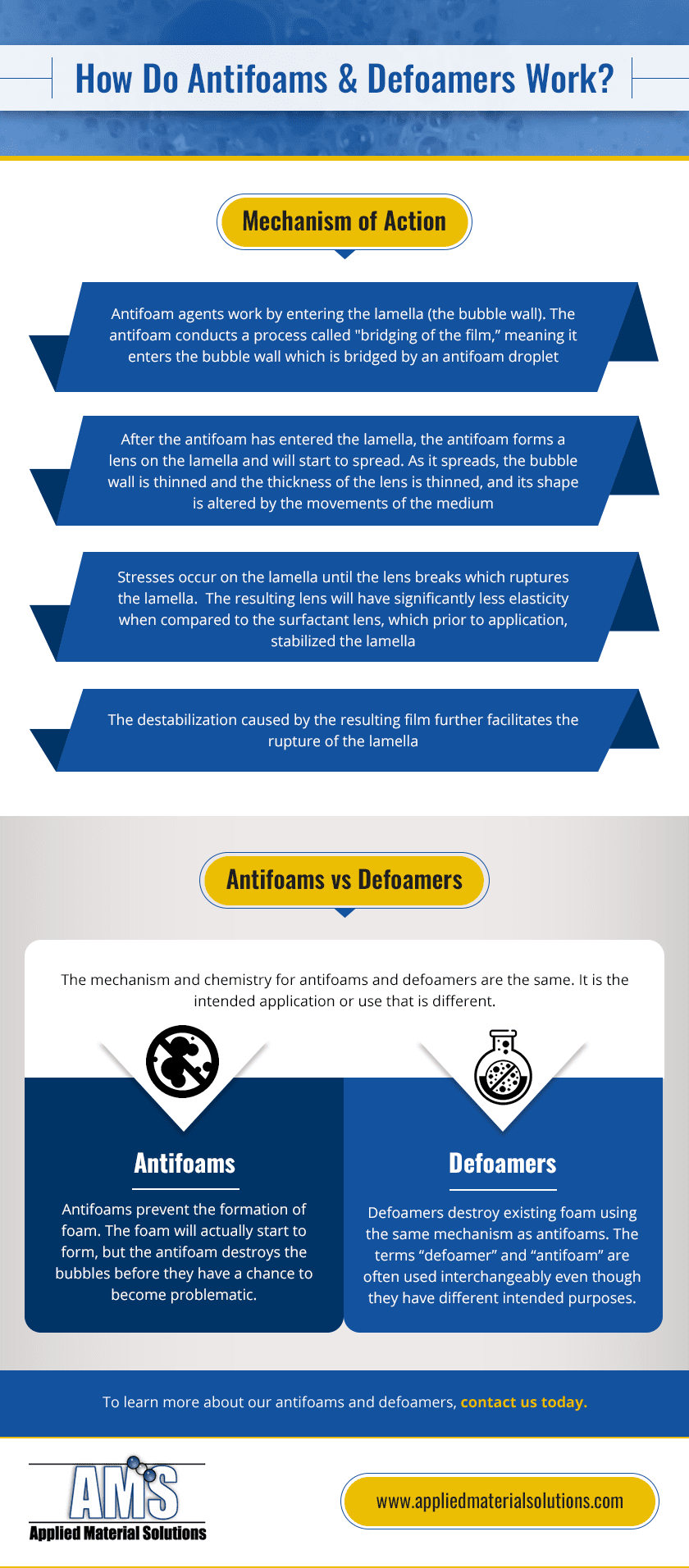
Picking the Right Defoamer
Choosing an ideal defoamer is essential for making the most of efficiency and quality in manufacturing processes. The selection of defoamer relies on various factors, including the specific application, the kind of foam being created, and the solution of the item being produced.
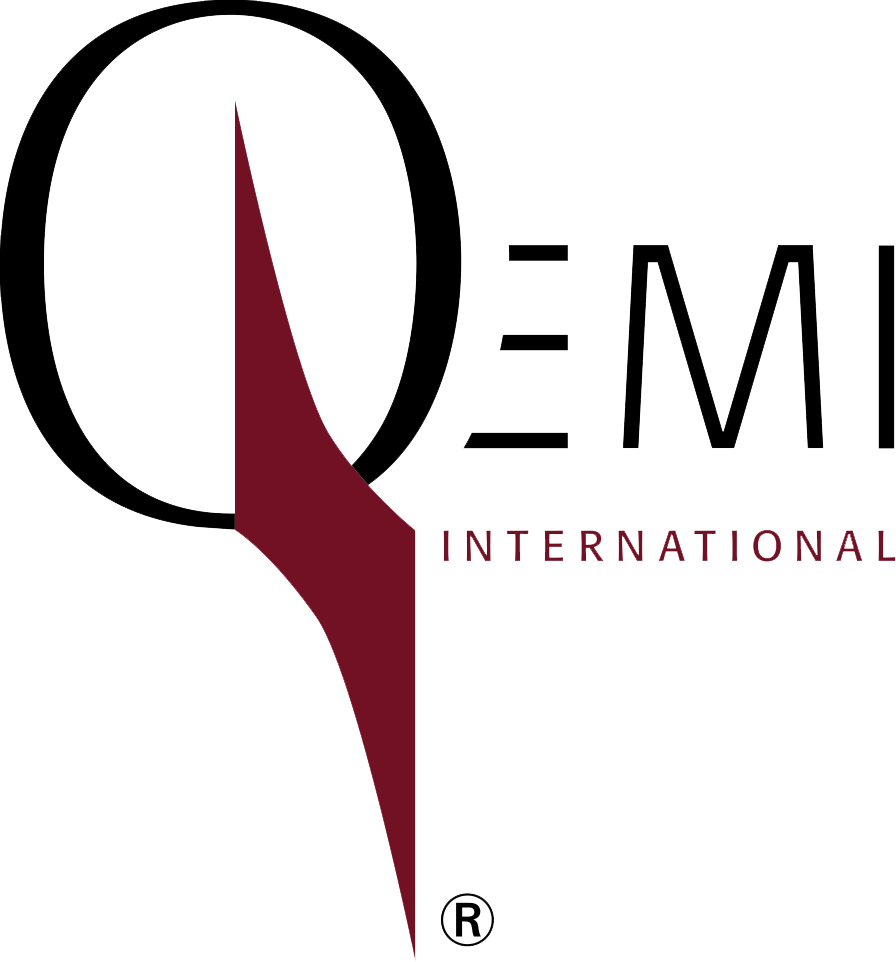
Firstly, consider the chemical compatibility of the defoamer with other components in your formulation. A defoamer that communicates negatively with other components can detrimentally influence product quality. In addition, the temperature and pH range throughout handling visit this web-site are vital; some defoamers do optimally under particular conditions while becoming inefficient in others.
Secondly, review the defoamer's efficiency qualities, such as its ability to swiftly decrease foam and its perseverance during manufacturing. It is necessary to choose a product that not just gets rid of foam swiftly however additionally preserves its performance in time.
Last but not least, take into consideration environmental and governing factors, especially if your production process undergoes stringent conformity standards. Choosing a low-toxicity or eco-friendly defoamer can help satisfy sustainability objectives while ensuring functional effectiveness. By attentively evaluating these standards, producers can make educated choices that enhance performance and item integrity.
Finest Practices for Execution
Successful application of defoamers in making procedures calls for careful planning and adherence to finest methods. It's important to carry out a detailed assessment of the production atmosphere. This includes understanding the particular application, the types of frothing representatives existing, and the functional conditions. Picking the ideal defoamer, as formerly discussed, is important; guarantee it works with the materials entailed and addresses the determined lathering problems successfully.
Next, keep clear interaction with all stakeholders, including operators and top quality control groups. Training sessions can help ensure that everyone recognizes the application procedures, potential effect on item quality, and safety factors to consider. Implementing a test stage can also be advantageous; monitor efficiency carefully to click here to find out more gauge performance and make essential modifications.
Additionally, normal testing and surveillance of foam degrees can offer valuable understandings into the defoamer's performance gradually. Adjusting does in reaction to adjustments in production variables will certainly assist keep optimal performance - defoamers. Recording all processes and results advertises continuous enhancement, allowing for fine-tuning of defoamer usage and improving total productivity in producing procedures.
Final Thought
In recap, defoamers play a critical function in enhancing effectiveness within production and production processes. By reducing foam formation and promoting bubble coalescence, defoamers add to enhanced product high quality, consistency, and operational performance. Their application throughout various markets emphasizes their versatility and significance in enhancing source use and lowering handling times. Inevitably, the strategic implementation of defoamers allows makers to raise manufacturing ability effectively, that site thus satisfying consumer assumptions and achieving cost savings.
The advantages expand to item high quality and expense savings, as defoamers help enhance procedures.Defoamers play an important function in various manufacturing processes by properly combating the development of foam, which can interfere with procedures and influence item high quality. Comprehending the buildings and features of defoamers is crucial for makers aiming to enhance their procedures, improve productivity, and keep the stability of their products.
Making use of defoamers in producing processes supplies a variety of significant advantages that improve operational effectiveness and product quality.In addition, defoamers enhance item consistency by avoiding air entrapment, which can endanger the stability of the last product.
Report this page